Milling
is today the most competent,
productive and
flexible-manufacturing methods for
complicated or sculptured surfaces.
Ball end tools are today used by the
manufacturing industry for the
machining of 3D free-form surfaces
for dies, molds, various parts, such
as aerospace components, etc.
Milling data, such as surface
topomorphy, surface roughness,
non-deformed chip dimensions,
cutting force components and dynamic
cutting behavior, are very helpful,
especially if they can be
computationally accurately produced
by means of a simulation program. |
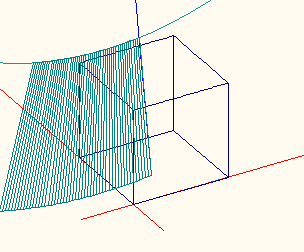 |
Face
Milling is today the most effective
and productive manufacturing method
for roughing and finishing large
surfaces of metallic parts. Milling
data, such as surface topomorphy,
surface roughness, non-deformed chip
dimensions, cutting force components
and dynamic cutting behaviour, are
very helpful, especially if they can
be accurately produced by means of a
simulation program. This paper
presents a novel simulation model
which has been developed and
embedded in a commercial CAD
environment. The model simulates
precisely the tool kinematics and
considers the effect of the cutting
geometry on the resulting roughness.
The accuracy of the simulation model
has been thoroughly verified, with
the aid of a wide variety of cutting
experiments. The proposed model has
proved to be suitable for
determining optimal cutting
conditions for Face Milling. The
software can be easily integrated
into various CAD-CAM systems. |
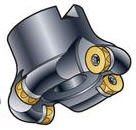 |