The
basic principle of the laser engraving process is that through
laser beam pulses, a large amount of heat is imparted locally
into the material of the workpiece that must be removed in order
to cause its sublimation. Laser engraving process is based on
the laser ablation process of the materials. During the laser
ablation process a laser beam pulse hits the surface of the
workpiece material, providing a large amount of focused heat
energy first causing melting, then vapourization-ablation and
finally the removal of ablated target material in the form of
vapour. When a sequence of continuous laser beam pulses is
scanned over the workpiece, the overall ablated material that is
removed produces a 3D geometry with a specific thickness, which
is called a single pass removed layer. By making multiple passes
with a predefined geometry on each layer, 3D geometries are able
to be engraved over the workpiece.
A 3D simulation model for
nanosecond pulsed laser engraving process is developed, using
the Finite Element Method (FEM) aiming at the prediction of the
final geometry of the workpiece and optimizing the process.
The development of a precise and reliable
simulation model is particularly important as it will enable the
ability to study the effect of material properties and the
process parameters on dimensional accuracy, manufacturing
quality and machining time.
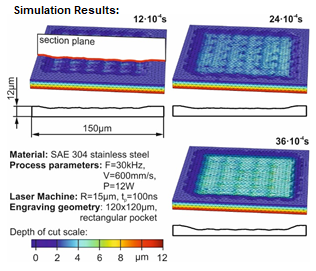
Simulation
test results for the case of engraving a 0.12x0.12mm rectangular
pocket with F=30kHz, V=600mm/s, P=12W laser process parameters.
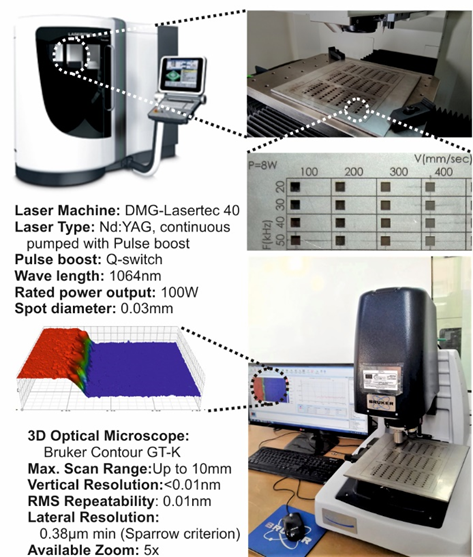
In order to verify the simulation model a large
set of experiments was performed for the purpose of comparing
the experimental with the simulation results. For this purpose,
laser engraving process experimental samples were conducted
using a DMG MORI Lasertec 40 machine for some widely used
materials using a wide range of process parameters.
Your contact:
Evangelos Nikolidakis
Tel.: +30 28210
37483
Mail:
enikolidakis@isc.tuc.gr
|